Medical device reprocessing (MDR) supports surgical quality assurance and mitigates risk
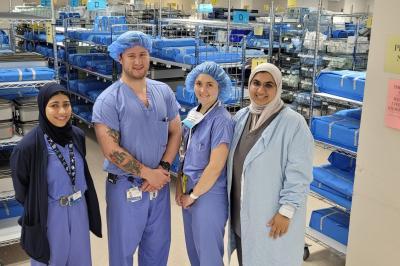
The medical device reprocessing (MDR) department at the Halifax Infirmary site of the QEII Health Sciences Centre, is tucked down a long corridor away from the noise and traffic of busy patient care areas. Despite its remote location, the space is open and bright with the sound of sterilizing equipment humming in the background.
Spread around the room, medical device reprocessing technicians (MDRTs) are situated at large steel tables with illuminated magnifying lamps examining instruments, preparing them for sterilization and packaging them in trays that are set-up with the devices needed for various types of procedures and surgeries.
“When assembling a tray, we are looking for cleanliness and functionality, to make sure instruments are in proper working condition. We test everything and verify information on how to sterilize by the manufacturer’s instructions,” said Becky White, supervisor at the Halifax Infirmary Medical Device Reprocessing Department.
Quality assurance in MDR is vital to ensuring staff and patient safety and taking the steps needed to prevent infections. The first step is to have technicians in the department who have completed a course in medical device reprocessing. Medical device reprocessing technicians work in MDR departments across the province, but they can also be found in various clinics reprocessing flexible scopes.
The team at the Halifax Infirmary provides practicum placements for technicians in training, to offer them hands on learning experiences. Technicians learn everything from decontamination procedures, quality assurance testing of equipment, inspecting and preparing sets and trays, sterilization and how to pick the case carts for surgeries. Staff are trained to reprocess reusable medical devices for all services including general surgery, orthopedic surgery and more.
The MDR department follows strict quality assurance protocols to ensure equipment is sterile and ready for surgeries and other procedures. This includes every instrument tray being packed with a special test strip. The small strips have a chemical dot that will become a solid black line to indicate that the items packaged within have met all the parameters required for sterilization -- time, temperature and exposure to the sterilizing solution. The test strip signals to team members opening packages in the operating room that items have been properly prepared and are safe for the patient.
“We also run a biological indicator (BI) test which includes a type of bacterial spore (Geobacillus Stearothermophilus) that is harder to kill than other microorganisms that might be present on medical devices. This test reads negative if the sterilizer kills the spores. We run these in every type of sterilization cycle we use and while the national standard requires us to run one BI per day, our safety measure is to run a BI in every third load because of the volume of instruments that come through our department,” says Becky.
The Halifax Infirmary medical device reprocessing department is staffed by 68 technicians and 11 utility workers. This skilled and well-coordinated team supports surgical teams 24-hours a day receiving incoming instrument carts from completed surgeries, preparing for scheduled surgeries and ensuring surgical trays are on hand to support emergency cases. The complexity involved in processing multiple instruments, where manufacturer instructions can be up to 200 pages, requires staff working diligently to ensure all the critical points have been adhered to.
The relationship between MDR and surgical teams is important in quality assurance of the instruments and patient care. The MDR team regularly provides tours to surgeons, residents and nurses to spend time in the space and get to know what happens to their instruments before and after surgery and the importance of the role they play in patient safety.
Advantages of spending time in MDR:
- Learn how to determine the steps for reprocessing reusable instrumentation, following manufacturer’s instructions
- Understand the differences between the chemicals used in the cleaning and disinfection of reusable devices
- Understand how to identify sterile instruments and what to look for inside the packaging • Awareness of quality assurance testing done in MDR
- Knowledge of end user responsibilities, including steps required at the point of use to protect items and prepare items for reprocessing